3D Printing Technology
Additive manufacturing, often referred to as 3D printing, revolutionizes production with its layer-by-layer construction method, enabling the creation of intricate designs and complex geometries while offering versatility in material choices ranging from plastics and metals to ceramics and even biological substances. This technology accelerates product development cycles, reduces material wastage, and fosters innovation, particularly in industries like aerospace, automotive, healthcare, and fashion. Its applications in the medical field include personalized implants, prosthetics, and organ printing. 3D printing empowers designers and engineers to push boundaries, creating structures previously deemed impossible, and its cost-effectiveness in low-volume production scenarios makes it appealing for small-scale manufacturers and startups. Collaboration between industries and academia propels research and development, while improved software tools ensure precise control over printing parameters, resulting in high-quality output. Regulatory bodies are adapting to accommodate 3D-printed products, recognizing their importance in modern manufacturing. Sustainability is a key advantage, as it enables recycling of materials and promotes a circular economy. As materials science advances, the range of printable materials continues to expand, unlocking new applications. In conclusion, additive manufacturing through 3D printing represents a transformative force in modern manufacturing, offering unparalleled flexibility,customization, and efficiency.
Types of 3D Printing and Its Processes
Fused Deposition Modeling (FDM)
​
An FDM printer operates by depositing layers of plastic filament onto a build platform, gradually creating physical models. It's an efficient and speedy method for producing tangible prototypes. While FDM can be used for practical testing in some cases, its utility is limited due to parts often having rough surface finishes and lacking durability. This 3D printing technology employs Material Extrusion, which is accessible and cost-effective. Here's how it works: a spool of solid thermoplastic material (such as PLA, ABS, PET) is loaded into the printer and fed through a heated nozzle, where it melts. The printer's extrusion head then moves along specific paths, depositing the material onto a build platform where it cools and solidifies, forming a solid object. This process continues layer by layer until the object is complete. Common applications of FDM include creating electrical housings, conducting structure and fit tests, making jigs and fixtures, and producing investment casting patterns. One of the advantages of FDM is its ability to provide good surface finish and full color options, along with the availability of various materials for different purposes.
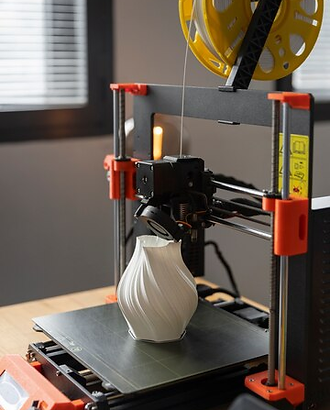

STEREOLITHOGRAPHY (SLA)
Chuck Hull introduced the world's first 3D printing innovation in 1986, pioneering a technique known as Vat Polymerization. This method involves selectively solidifying a material called photopolymer resin using a light source. Stereolithography (SLA) emerged as the first modern 3D printing process. SLA printers excel in achieving high levels of detail, smooth surface finishes, and precise tolerances, making them particularly valuable in the medical industry for creating anatomical models and microfluidic devices.
In SLA printing, mirrors called galvanometers are employed, with one positioned on the X-axis and the other on the Y-axis. These mirrors direct a laser beam across a reservoir of resin, selectively curing and solidifying a cross-section of the object in the build area, layer by layer. SLA is a rapid prototyping process that prioritizes precision and accuracy, capable of producing objects from 3D CAD data in a matter of hours.
During the printing process, fluid photopolymers are converted into solid 3D objects, with each layer meticulously constructed using a UV laser guided by scanning mirrors. A recoater blade ensures even distribution of the resin across the object's surface before each layer is solidified. Upon completion, the 3D part typically undergoes a chemical bath to remove excess resin and may be post-cured in a UV oven for enhanced strength and stability.
SLA printing has found widespread application across various industries including automotive, medical, aerospace, entertainment, and consumer goods manufacturing. Popular SLA printers such as Vipers, ProJets, and iPros 3D printers, manufactured by 3D Systems, are commonly used in these sectors.
Specific laser sintering (SLS)
Chuck Hull introduced the world's first 3D printing innovation in 1986, pioneering a technique known as Vat Polymerization. This method involves selectively solidifying a material called photopolymer resin using a light source. Stereolithography (SLA) emerged as the first modern 3D printing process. SLA printers excel in achieving high levels of detail, smooth surface finishes, and precise tolerances, making them particularly valuable in the medical industry for creating anatomical models and microfluidic devices.
In SLA printing, mirrors called galvanometers are employed, with one positioned on the X-axis and the other on the Y-axis. These mirrors direct a laser beam across a reservoir of resin, selectively curing and solidifying a cross-section of the object in the build area, layer by layer. SLA is a rapid prototyping process that prioritizes precision and accuracy, capable of producing objects from 3D CAD data in a matter of hours.
During the printing process, fluid photopolymers are converted into solid 3D objects, with each layer meticulously constructed using a UV laser guided by scanning mirrors. A recoater blade ensures even distribution of the resin across the object's surface before each layer is solidified. Upon completion, the 3D part typically undergoes a chemical bath to remove excess resin and may be post-cured in a UV oven for enhanced strength and stability.
SLA printing has found widespread application across various industries including automotive, medical, aerospace, entertainment, and consumer goods manufacturing. Popular SLA printers such as Vipers, ProJets, and iPros 3D printers, manufactured by 3D Systems, are commonly used in these sectors.
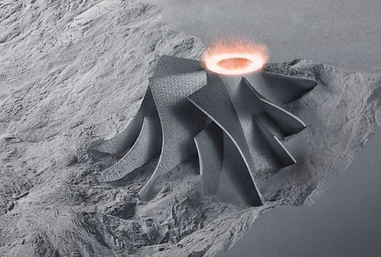
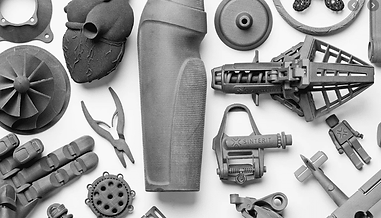
PolyJet
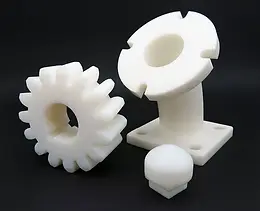
PolyJet 3D Printing is a cutting-edge technology that swiftly produces accurate parts utilizing photopolymers, UV light, and inkjet heads. Its precision lies in layering resins to create digital materials. The process begins with converting a CAD model into a printable format. Photopolymer droplets are sprayed onto the build platform, then cured with UV lamps to fuse layers. Support materials are dissolved or manually eliminated to achieve the final PolyJet model.
Digital Light Process (DLP)
DLP boasts faster print times compared to SLA because each layer is exposed simultaneously, rather than tracing the cross-section of an area with a laser. Common applications for both SLA and DLP include polymer models for injection molding, jewelry, dental use, and lenses. They feature intricate details and a smooth surface finish. However, they are limited by their brittleness, making them unsuitable for mechanical parts.
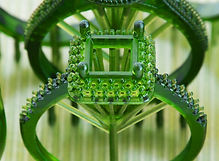
Multi Jet Fusion (MJF)

Multi Jet Fusion constructs functional parts from nylon powder. Instead of laser sintering, MJF employs an inkjet array to apply fusion agents to the nylon powder bed. Then, heat fuses each layer, ensuring consistent mechanical properties and enhanced surface finish compared to SLS. MJF's accelerated build time leads to lower production costs. It differs from other 3D printing methods, which deposit, sinter, or cure build material point by point. MJF jets droplets of photopolymer, curing them with UV light. Layers are deposited and cured successively until the object is complete. Unlike other methods, MJF deposits material in a fast, line-wise manner. Support is provided during printing using a dissolvable material, removed post-processing. MJF uniquely accommodates multiple materials and full-color printing. With proper arrangement and spacing, it achieves faster production than other methods, offering versatility for various projects. Selecting the optimal process is crucial for project success.
Direct metal laser sintering (DMLS)
Direct Metal Laser Sintering (DMLS), also known as Selective Laser Melting (SLM), is a prevalent additive manufacturing method. It fabricates each part layer by directing a laser at specific points on a powder bed, guided by a CAD file. After printing a layer, more powder is spread, repeating the process. DMLS excels at creating precise, high-resolution parts with intricate geometries. It uses a laser to digitally heat the powder to its melting point, eliminating the need for physical molds. The resulting parts boast accuracy, excellent surface quality, and near-wrought mechanical properties.
DMLS printers are recommended for producing industrial items with challenging features like hollow spaces and complex angles, which are difficult or impossible to fabricate otherwise. Ideal for low-volume production, DMLS saves time and expenses associated with tooling creation. Parts can be stored digitally and printed on demand, reducing inventory costs and enhancing design flexibility.
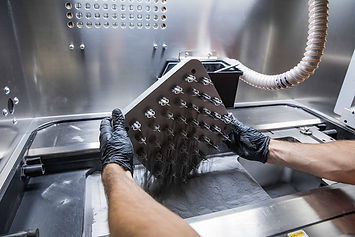
Electron Beam Melting (EBM)

Electron Beam Melting (EBM), a member of the powder bed fusion family, employs an electron beam to fuse metal particles layer by layer, unlike Laser Powder Bed Fusion (LPBF). Introduced by Swedish company Arcam in 2002 and now under GE Additive, EBM creates intricate and highly durable structures. The key distinction lies in the heat source: EBM utilizes an electron gun to generate an electron beam, which selectively fuses metallic powder on the printer's build plate. This process enables the production of complex parts with exceptional strength and resilience.